17 October 2023
RME deploys world’s first system for relining from outside the mill
RME today announces that it has successfully deployed the world’s first roboticised mill relining system that enables safer, faster worn liner removal and new liner placement with no one inside the mill.
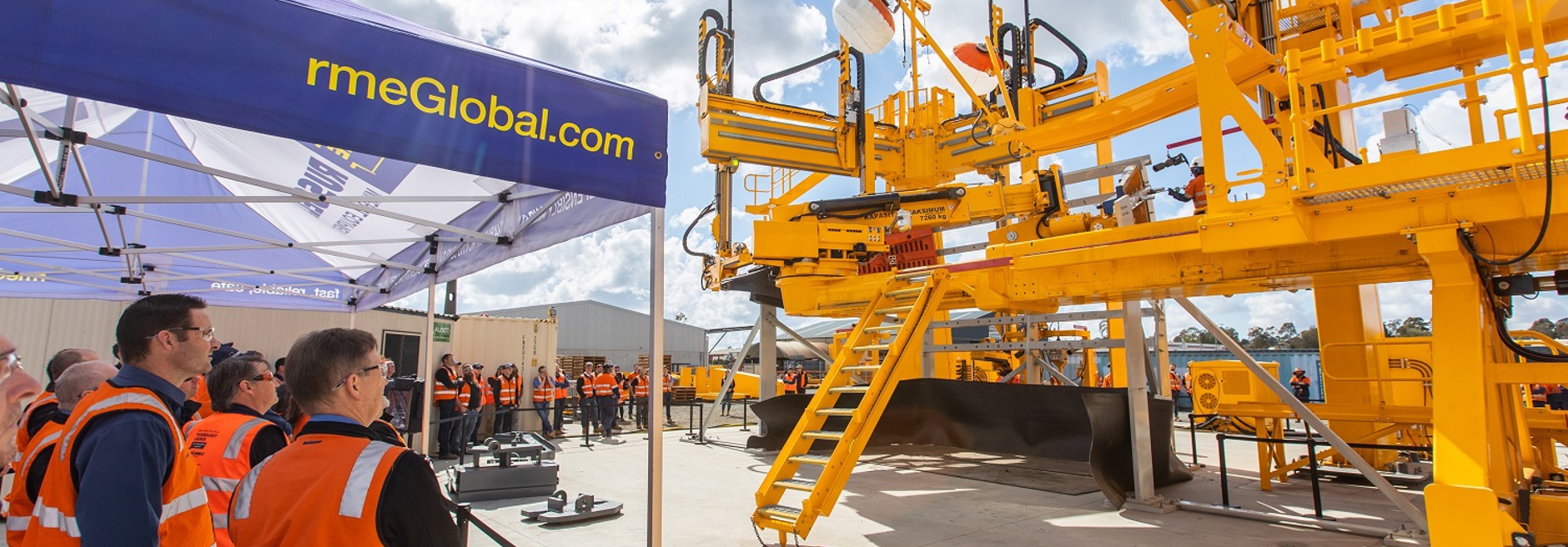
Mill relining systems manufacturer, RUSSELL MINERAL EQUIPMENT (RME) has deployed the world’s first semi-automated mill relining system, delivering significant safety and commercial outcomes for its Customer and the wider industry.
The reduction in mill relining risks and shutdown duration was achieved through a powerful combination of: roboticising RME’s mature and proven technologies; compatible liner and bolt design; and strong collaboration and change management with site management and reline crews.
RME’s automated system addresses the two main phases of mill relining: worn liner removal and new liner placement, and enables the completion of these necessary maintenance processes without anyone inside the mill. This system was developed and implemented in close collaboration with some of RME’s existing Customers, including PT Freeport Indonesia.
Safely, consistently and repeatably speeding up mill relining
RME Founder, Executive Chairman and Chief Engineer, Dr John Russell describes the new paradigm for fast, automated mill relines as the ultimate in safety and improved commercial performance for concentrators.
“RME’s goal has been to enable our Customers to reline mills with no one inside, providing them with remarkable safety and efficiency benefits. By eliminating human-machine interaction, we can speed up the machines and relining processes, consistently and repeatably. This advanced capability is now a reality ”
“We are grateful to our Customers, and to our liner and bolt technology partners, for their shared commitment to achieving these results. I would also like to recognise and thank our team at RME who has made our shared vision a reality.”
An automated system that is greater than the sum of its parts
The remarkable results achieved to date can be attributed to RME’s systems engineering approach. Safety inside and outside the mill was the priority and every step was carefully reviewed according to RME’s 24 Steps to Mill Relining Standard.
“We understood from our 35+ years as an OEM that to safely automate mill relining, we would need to consider the many interdependent tasks across the entire process,” added Dr Russell.
“The engineering result is now a tightly-integrated system of advanced modular technologies that automate manual repetitive tasks, eliminate risks and speeds-up relining.”
Consequently, RME’s automated system enables a staged implementation whereby upgrades happen within planned maintenance windows over multiple reline events. This ensures Customers will not experience additional costly mill downtime scenarios.
Roboticising established technologies minimises risks
One major advantage of RME’s semi-automated mill relining system is that its underpinning technologies are well-established and well-used by the industry.
Dr Peter Rubie, who held the role of Chief Engineer at RME until 2019 and is a non-executive director at RME, played a key role in the development of the company’s automation technologies.
“Mining can be conservative when adopting new technologies, due to economic risk,” said Dr Rubie.
“For some of our Customers, even one hour of downtime can cost upwards of US$200,000 of production. We can avoid these impacts by automating existing proven systems.
“The beauty of RME’s mill relining technologies ecosystem is that the elements are modular and future-proofed. Miners of all sizes can deploy the base components and then incorporate additional automation steps at their own pace.”
The centrepiece of RME’s semi-automated mill relining system – the RUSSELL 7 Model R AutoMotion™ Mill Relining Machine (MRM) – is a highly advanced configuration of the industry’s most adopted 7-axis liner exchange machine, the RUSSELL 7 MRM.
It is complemented by THUNDERBOLT SKYWAY, a semi-automated knock-in system used on the exterior of the mill. Operational since 2020 at sites in Central America and Indonesia, SKYWAY is well-proven. This technology is now also available as a portable lift-in solution called THUNDERBOLT SKYPORT. It is another automation of RME’s established technology that increases asset utilisation by being sharable between mills onsite.
These systems, working together with INSIDEOUT™ Technology tooling and compatible liner and bolt design, can grab knocked-in worn liners off the shell or from the charge, and place new liners against the shell with millimetre precision, and without personnel working inside the mill. The securing of liners, nuts and bolts from the mill’s exterior can also now be achieved using RME BOLTBOSS.
Engineering the risk out of mill relining
RME has been collaborating with Customers across several sites to progressively automate mill relining, including upskilling their Customers’ local crews.
Analysis of historical reline shutdown data using conventional relining methods, compared with filmed data using some, but not all, of RME’s automated mill relining technology suite, reports a 56% risk reduction for activities inside the mill and 30% productivity uplift for a 38’ SAG mill.
Following a staged implementation, PT Freeport Indonesia recently completed their first reline utilising the combination of THUNDERBOLT SKYWAY and the RUSSELL 7 Model R AutoMotion™ MRM.
While the performance data is currently being analysed, early indications point to an even greater reduction in risk and increase in productivity than was originally targeted.
Director Metallurgy and Strategic Planning at Freeport-McMoRan (FCX), Dr John Wilmot summed up the outcomes FCX are seeing as safer and faster mill relining at the recent SAG 2023 conference in Vancouver, Canada.
“PT-FI Indonesia has largely removed crew from inside the mill as we reline. While there are still a few residual activities where we need to enter, such as wash-down, we’re executing relines faster and safer than before. Mill relining is no longer on the critical path.”
“RME’s modular systems approach enabled us to progressively implement the technology, which meant we could quantify the safety and productivity improvements at each reline event, even as the new technology was being deployed.
“The staged implementation also provided an opportunity to create strong buy-in from our reline crew. In our experience, when the crew is part of the optimisation journey, the change program is infinitely more successful. At PT-FI Indonesia, our reline crew has now taken full ownership of the process.”
“Leveraging RME’s equipment and methodologies, as well as the compatible liner and bolt designs, our crew has experienced the difference that automation can make. They’ve found it to be safer and faster, and they won’t go back to conventional methods. We’re incredibly proud of their work. By collaborating closely with all the stakeholders involved, we are engineering the risk out of mill relining.”
“We believe RME’s collaborative and staged approach can serve as a model for the mineral processing industry,” added Dr Russell. “It is already achieving step-changes in safety and mill availability for our Customers and we’re excited to see the impact it may have industry-wide.”
A solution to help our industry and the planet
For more than 35 years, RME has dedicated itself to making grinding mill relining safer and faster.
RME’s semi-automated mill relining system will also help Customers meet the growing demand for copper and the other critical minerals required in the transition to net zero.
Dr Russell described it as a solution for our industry and a solution that he hopes is equally good for our planet.
“We have now completed more than 30 real world relines using the various products of RME’s Advanced Technology suite,” said Dr Russell.
“It gives me the confidence to present our system as the safest solution for our industry.
“And the data we’re seeing from the 30-plus relines, gives me the confidence to state that this system better for productivity.
“The transition to net zero requires an enormous increase in the minerals that are essential to the decarbonisation of our economies.
“We are delighted to be able to play a part in safely speeding up the production of those minerals.
“We’ve achieved these results in partnership with our Customers, using the same pioneering mindset with which we’ve approached the past 35 years.”
For more information about RME Advanced Technology visit www.rmeglobal.com/what-we-do/optimisation-partnering/rme-advanced-technology/
About RUSSELL MINERAL EQUIPMENT
RUSSELL MINERAL EQUIPMENT (RME) is the world’s leading Mill Relining Systems Technology supplier. We invent machine systems and service-based solutions for problems encountered in the world’s mining and mineral processing industries. Our technologies deliver short shutdowns, high mill availability and safe working environments. Established in 1985, RME has grown to operate in 64 countries, has 12 international Sales and Service Centres and employs more than 450 people worldwide. For more information visit www.rmeglobal.com.