30 October 2023
In conversation with industry leader, Dr John Russell
RME's Founder and Chief Engineer, Dr John Russell, speaks about the company’s pioneering efforts to enable relining from outside the mill and its impact on the future of mineral processing.
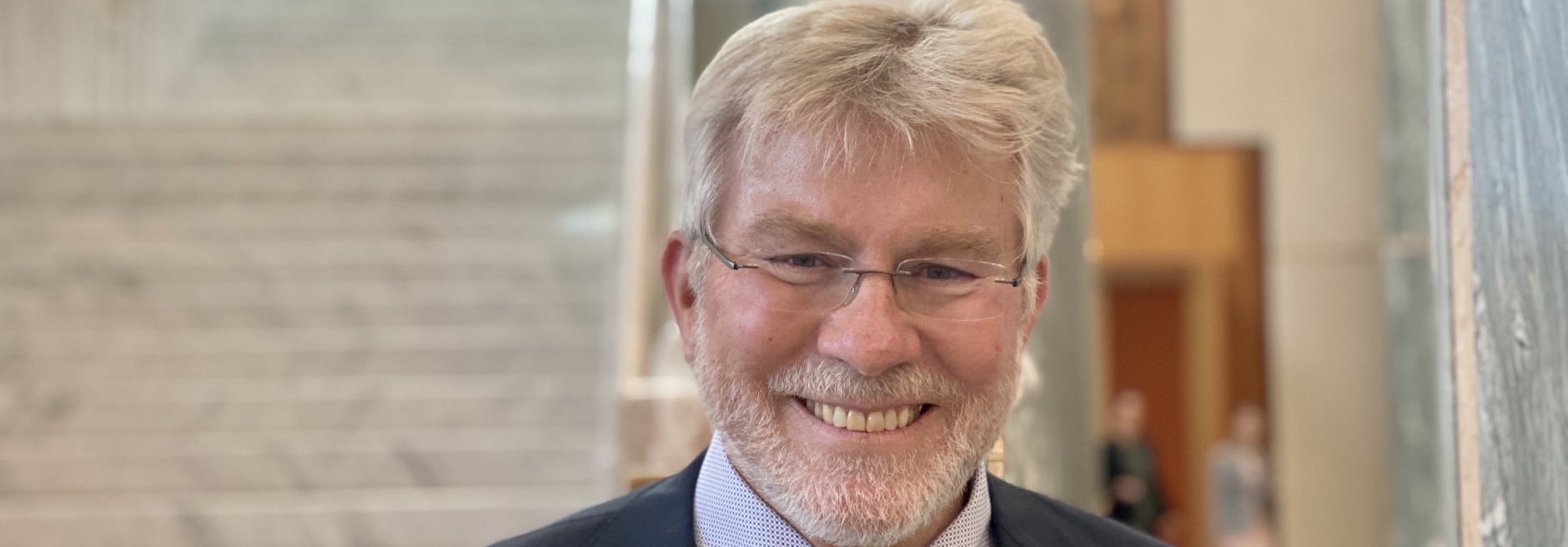
RUSSELL MINERAL EQUIPMENT (RME) is pioneering mill relining automation for a safer and more efficient future for mineral processing.
Focused on reducing risk and improving efficiency, RME aims to eliminate the need for reline crews to work inside the confined-space mills during relining, while also helping to unlock greater mill availability to meet the growing demand for minerals like copper and iron ore.
Recognising the importance of technical risk, system integration and change management, RME’s approach has been to build upon confidently-used, established technologies and processes, strong collaboration with Customers, reline crews, liner and bolt suppliers, and extraordinary efforts from RME’s engineering team.
RME Founder, Executive Chairman and Chief Engineer, Dr John Russell spoke with RME's Marketing Team about the journey so far and the potential of this fast-emerging technology.
Q1: Why is mill relining automation important for the industry?
Q2: What parts of the process have been automated?
Q3: The importance of 'systems engineering'
Q4: Overcoming technology implementation risks
Q5: Key automation-enabling technologies
Q6: Implementation sequence
Q7: Commercial outcomes
Q8: Site safety and performance data so far
Q9: Reline crew buy-in
Q10: Early and majority industry adoption
Q11: Closing statements
1. Thank you for joining us today Dr John Russell. To start us off, could you share why automating mill relining is crucial for the mining industry?
John Russell: For most concentrator plants, relining is still a critical path maintenance process, and delays can have economic consequences for mill availability and production. For most operations, mill relining still holds some risk to personnel, albeit reduced through our RME Mill Relining System.
RME has long aimed to eliminate the need for personnel to work from inside the mill during relining by harnessing automation. This is because we see that automation delivers a threefold advantage. Firstly, it improves crew safety by eliminating human-machine interaction. Secondly, it removes performance variability associated with manual machine operation, making for more predictable reline durations. Thirdly, removing personnel from inside the mill creates an environment that allows us to increase the speed of the mill relining machines – consistently and repeatably.
This leads to shorter shutdowns, higher mill availability, and ultimately increased production capacity. It has the potential to be a game-changer for the safety and commercial performance of mineral concentrators.
2. Can you provide an overview of the automated system developed by RME and its significance for the industry?
John Russell: Certainly. In simple terms, we’ve roboticised the existing and familiar ‘RME Mill Relining System’ – our integrated suite of technologies that assists with every step of the mill relining process. Automation has been applied primarily to mill relining’s two main phases – worn liner removal and new liner placement.
Automating these phases now enables mill relining to be performed with no one inside the mill during liner movements and allows for consistently faster machine movements. What I love is that operators can use the RUSSELL Mill Relining Machine conventionally and then deploy automation progressively, as their confidence grows. It’s not ‘all or nothing’. It’s a flexible implementation model and importantly it’s a flexible commercial model too.
If automation can deliver a 1% improvement (or 87 hours) in annual mill availability for a mill-constrained plant, it could generate an additional US$ 9m-18m in annual production value per annum, ensuring a rapid return on investment.
Importantly, this achievement has been the result of strong industry collaboration. We’ve worked closely with safety-conscious Customers on the technology. We’ve also partnered with one of the world’s leading liner manufacturers to develop compatible liner designs that enable human-free interaction with the RUSSELL Mill Relining Machine, and worked with a bolt supplier on a methodology to secure nuts and bolts from outside of the mill.
3. Can you explain the systems engineering approach used by RME in developing the automated mill relining system, and how it contributed to the results achieved? How does it ensure safety and efficiency?
John Russell: We knew from our 35+ years as an OEM, that in order to safely automate liner exchange, we needed to consider the many interdependent tasks in mill relining.
Any change to relining on the outside of the mill had to account for the associated activities inside the mill, and vice versa. For instance, if we were to introduce a robotic machine that can reach greater heights outside the mill during knock-in without considering the implications for inside the mill, safety hazards can increase for the reline personnel inside.
To mitigate these risks, we took a holistic approach and reviewed every step in accordance with RME’s 24 Steps to Mill Relining standard. This led to the development of a tightly-integrated modular system that automates manual repetitive tasks, eliminates hazards and ensures safety and efficiency throughout the mill relining process.
4. How has RME addressed the mining industry’s cautiousness with regards to new technology adoption and potential downslides when trialing robotics in production environments?
John Russell: Mining operations rightly approach new technologies cautiously due to economic risks and complex factors like technical integration, safety and cultural resistance.
For some of our Customers, even an hour of extra mill downtime can cost upwards of US$200,000 in production. We understand and appreciate this caution so our solution addresses the causes.
RME’s solution succeeds because it lies in automating well-established and confidently-used, trusted technologies. By roboticising these proven systems, we avoid disruptions and economic impacts associated with the introduction of unfamiliar technologies and processes.
We’ve developed a carefully-staged and supported implementation program which minimises technical and cultural change risks. This allows Customers to adopt automation progressively, reducing the risks associated with large-scale technological shifts.
5. What are the key components of RME’s automated mill relining system?
John Russell: Think of our automated mill relining system as an integrated ecosystem of technologies and processes, which are already familiar.
I’ll start with the system’s centrepiece, which is an advanced configuration of the industry’s most widely used 7-axis machine for liner exchange inside the mill – the RUSSELL 7 Model R AutoMotion™ Mill Relining Machine, or MRM.
Complementing this is a semi-automated knock-in system on the exterior of the mill called THUNDERBOLT SKYWAY, which we are also making portable with THUNDERBOLT SKYPORT. SKYWAY is a proven system that has been operational at sites in Central America and Indonesia since 2020.
These technologies, along with specially-engineered INSIDEOUT™ Technology tooling such as the new award-nominated RUSSELL Claw, RUSSELL Forks Tool and RME BOLTBOSS, work together to remove and install new liners against the shell with millimetre precision — all from the mill's exterior and with no one inside.
6. You’ve mentioned a modular approach. Is there an ideal implementation sequence for deploying an automated mill relining system?
John Russell: The correct implementation sequence is important for both productivity and safety.
Consider two ‘organisational design’ fundamentals: firstly, enabling RME AutoMotion™ on the RUSSELL 7 Model R MRM is contingent upon removing all personnel from the mill during liner removal and placement activities, given the inherent risks of human-robotics interaction and because a roboticised MRM can move faster, with all seven axes of movement now synchronised in the MRM’s programming.
Secondly, making upgrade changes to technologies and processes within planned maintenance event windows, considering also that relining typically only occurs 2-3 times annually, limits available implementation time-frames.
So, recognising these fundamentals, we’ve have broken down the automation implementation process into manageable, logical steps, or modules. Initially we focus on worn liner removal, introducing technologies like SKYWAY to automate the operation of THUNDERBOLT Recoilless Hammers outside the mill. Then we add RUSSELL MRM grapple accessories like the RUSSELL Claw or RUSSELL Forks Tool, for remotely removing worn liners from the mill's shell or charge without personnel inside the mill.
Once the worn liner removal phase is automated, operators confidently progress to the new liner placement phase. This phase entails some adjustments to liner and bolt design, allowing the RUSSELL 7 Model R AutoMotion™ MRM to autonomously pick up new liners located outside the mill, transport them to the designated location on the mill shell along the most efficient path, and then precisely install them on the mill shell. Liners are then secured from outside the mill by crews using RME BOLTBOSS.
With these two phases now roboticised, we have a mill relining system where nobody enters the mill during liner exchange. And this progressive implementation approach I’ve described ensures mill operators experience tangible safety and productivity uplift, reline-by-reline, as the new technologies are being progressively deployed.
We’re also actively working on solutions for the few remaining tasks that require crew entry into the mill such as mill washdown.
7. You mentioned attractive commercial outcomes for mill operators. How can these outcomes be measured?
John Russell: RME’s Mission Statement ensures that improvements we help our mill operators make are visible, defensible and sustainable, so measurement of safety and performance gains is a critical element in our approach. We’ve developed a Discrete Event Simulation program called MILL RELINE DIRECTOR (MRD). It creates a ‘digital replica’ of a mill operator’s mill and reline operation. We then compare speed and safety performance, quantifying improvements from one reline to the next. MRD also allows us to model the impact of variations on mill availability and person-hours exposed to risk, answering important ‘what if’ questions. MRD allows mill operators to quantify the benefits of changes to their relines, build business cases to support investment and plan for organisational design changes.
8. Can you share specific performance data and results achieved with the automated mill relining system?
John Russell: We are very proud of the results that our committed and progressive Customers are having.
In our collaboration with a Customer in Indonesia, which has been focused on bringing their crews out of a 38' SAG mill during relining, we have observed some remarkable results.
Automating the liner removal phase has led to a 56% reduction in their risk exposure inside the mill and a 30% improvement in their liner replacement speed compared to conventional relining.
Furthermore, since automating the knock-in process, this site has reported no safety injuries during this phase of relining.
We've also just recently enabled RME AutoMotion™ on their RUSSELL 7 MRM for autonomous new liner placement, and while we're still analysing the performance data, early indications show even greater risk reductions and productivity gains. We have reason to believe that this site achieved a 'sub-50 hours' record for a high-wear reline—an outstanding performance—and we believe they can go even faster.
9. How have reline crews adapted to using the automated mill relining system? Has there been any resistance and how was this overcome?
John Russell: This is an important part of any ‘change’ process. It’s fair to say that in the very early stages there can be reluctance to using new technology, so we work with mill operators to address these concerns through training and education.
We did experience that our staged implementation program provided an opportunity to create strong buy-in from the reline crew. We want them to be part of the optimisation journey, rather than imposing change upon them. It’s about cultural and organisational leadership. It’s absolutely about committed safety leadership, too.
This approach has been successful, with the reline crews taking full ownership of the process and holding each other, and site management, to account for adherence to their new process. They have experienced the safety and speed benefits, and have no desire to return to conventional methods, viewing them as too unsafe.
10. Looking forward, how do you see the adoption of automated mill relining evolving in the mining industry?
John Russell: We anticipate that larger mills and longer-life mines will favour automated mill relining. High-altitude sites, in particular, will benefit due to improved fatigue management. Importantly, our technology is modular and future-proofed, allowing mines of all sizes to deploy base components and gradually advance their mill relining. It's a flexible approach that aligns with each mine's pace and requirements.
Early-adopter brownfield and greenfield sites have now completed over 30 relines using a range of RME’s automated mill relining technologies, so we expect mainstream adoption to significantly accelerate over the next few years.
We believe our approach can be a model for the entire mineral processing industry to achieve substantial improvements in safety and mill availability. The modularity of our system allows miners of all sizes to deploy base components and progressively mechanise and automate using a staged implementation program, ensuring a smooth transition. Ultimately, we hope to witness a safer and more efficient approach to mill relining industry-wide.
11. In summing up, what do you see is the significance of this achievement for the industry?
John Russell: These developments represent a significant milestone for the industry. Despite advances in mechanisation over the years, grinding mill relining remains the most dangerous maintenance task in mineral concentrators.
For over 35 years we’ve worked tirelessly to make relining safer, and today we know we can execute liner exchange with no one inside the mill.
This system not only enhances safety, but also contributes to faster mill relining and increased mill availability, accelerating the production of critical minerals for decarboniszing our economies.
RME’s ultimate goal of fast, safe automated mill relining is to enable the processing of more tonnes per year using the same or less energy, further contributing to sustainable practices in the mining industry.
It underscores our commitment to an industry that plays a critical role in meeting the world's demand for essential minerals while improving the well-being of those who make it happen.
Top
To learn more about RME's Advanced Technology Suite which is enabling relining from outside of the mill, click on the links below and reach out to your nearest RME International Sales and Support Centre.
Learn more about RME Advanced Technology
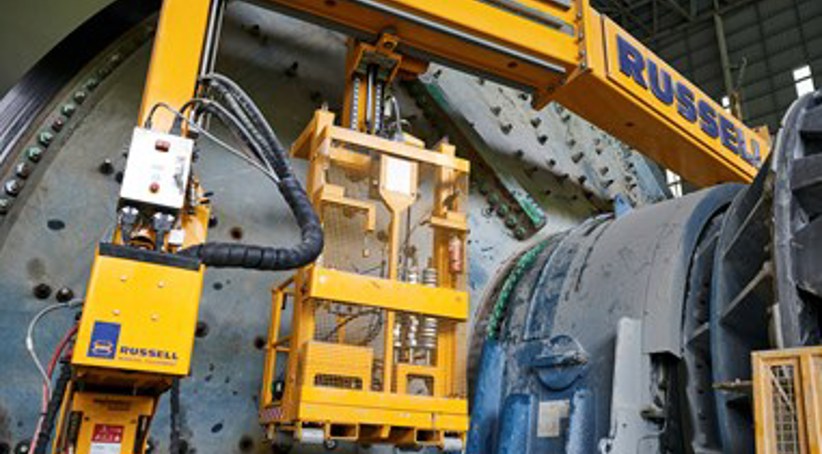
THUNDERBOLT SKYWAY
THUNDERBOLT SKYWAY roboticises the operation of THUNDERBOLT Hammers to vastly improve knock-in speed and safety – consistently, repeatably, sustainably.
Read more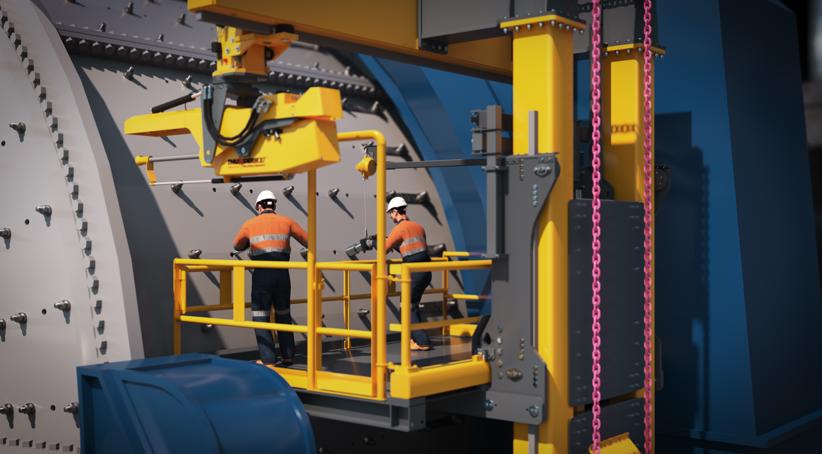
THUNDERBOLT SKYPORT
Portable and modular, THUNDERBOLT SKYPORT is the lift-in version of the fixed plant THUNDERBOLT SKYWAY, RME's semi-automated knock-in technology.
Read more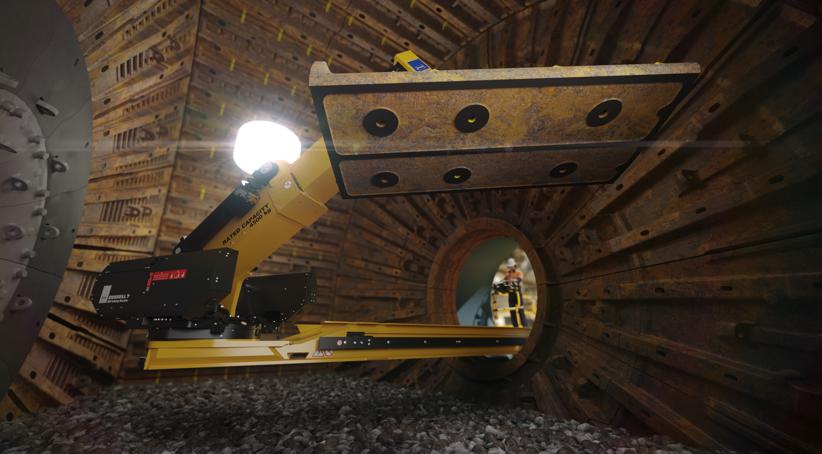
RUSSELL 7-R AUTOMOTION MRM
The world's first semi-automated mill relining machine for relining from outside of the mill.
Available in 4500 kg – 9000 kg capacities.
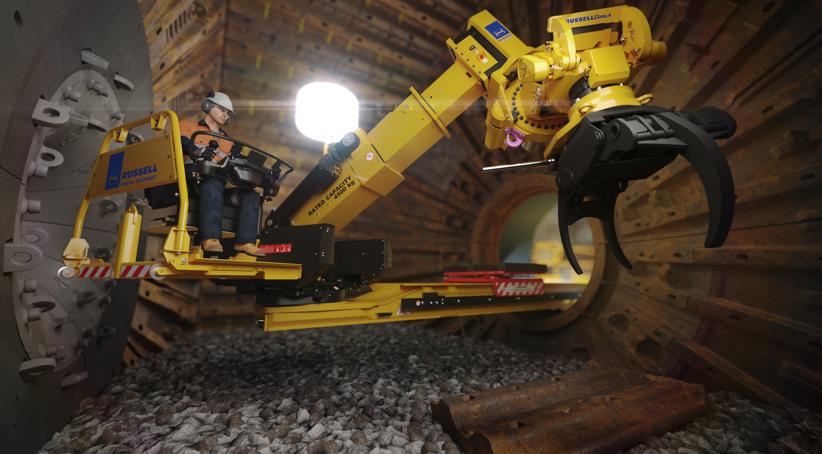
RUSSELL CLAW
Introducing the RUSSELL Claw – the new master of muck-out and eliminator of manual liner slinging.
Lifting capacity up to 8000 kg.
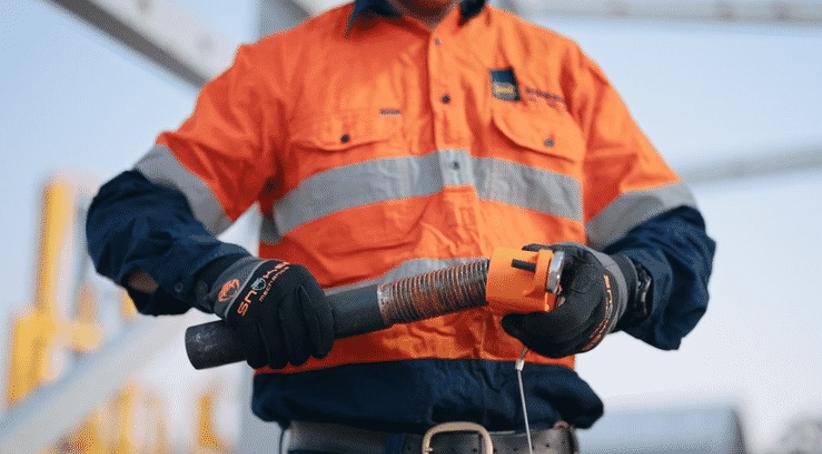
RME BOLTBOSS
RME BOLTBOSS is an innovative universal toolset that enables safer securing of liners, nuts and bolts from the mill’s exterior without the need for crew to be inside.
Read more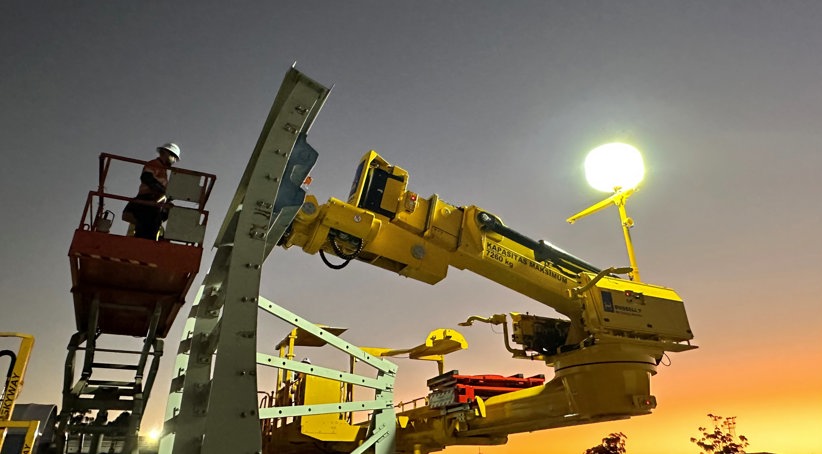
RME ADVANCED TECHNOLOGY
Our relentless pursuit to improve safety and productivity has driven us to engineer a future where relining is performed safely from outside the mill – at faster speeds than ever before.
Read more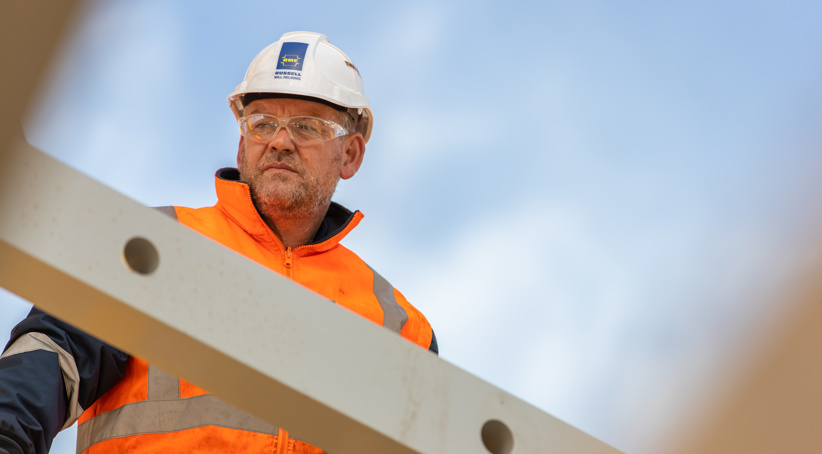
MILL RELINE DIRECTOR
MILL RELINE DIRECTOR (MRD) discrete event capture, analysis and 'digital twin' simulation provides clear line of sight into the complex process of mill relining.
Read more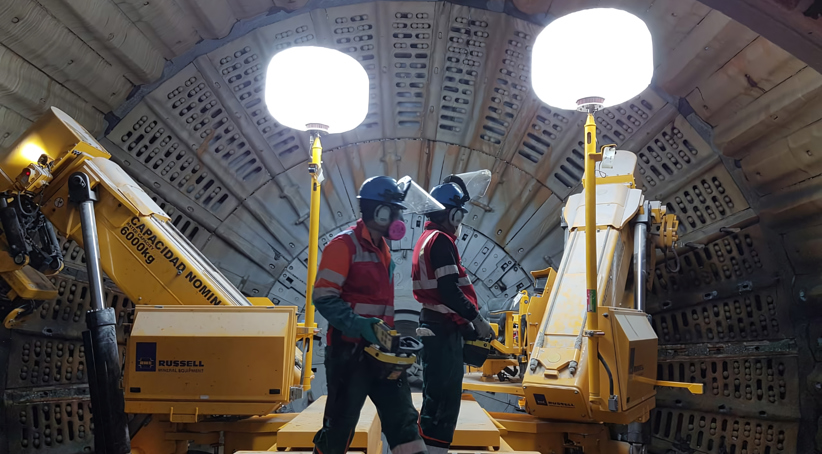
WE ARE HERE TO HELP
We ensure Customers have access to trusted OEM engineering know-how where and when they need it. Here's how to contact RME.